Développement d'un outil optimisé pour la préparation et l'analyse des matériaux poreux par RMN améliorée
Equipement, AAP 2018-4
Porteur : Patrick Berthault
Résumé :
L'objectif du projet est de proposer un outil performant et polyvalent pour l'analyse structurale de matériaux poreux, utilisant la fluidique (gaz et liquides) et la micro-RMN. Il tirera profit des récents développements instrumentaux basés sur la conception d’inserts imprimés en 3D. Ces inserts sont conçus pour être branchés sur une tête de sonde de micro-imagerie et connectés électriquement au circuit d’accord. Dans cette configuration, le micro-solénoïde est placé aussi près que possible du matériau à étudier. Un pousse-seringue placé sur l’aimant de RMN permet une distribution contrôlée de gaz ou de liquides dans le circuit. Cette configuration présente plusieurs avantages par rapport aux systèmes classiques, tels qu'un facteur de remplissage optimisé et une grande polyvalence, car tous les noyaux peuvent être étudiés simplement en modifiant les valeurs du condensateur.
Cependant, actuellement ces expériences ne peuvent pas être réalisées à des températures élevées ou avec des liquides plus corrosifs que l’eau, ce qui limite considérablement la gamme d’études accessibles. Nous développerons donc le même principe d’insert, mais en céramique ou en verre imprimés en 3D. En effet, des publications récentes ont donné des pistes pour construire de tels inserts en utilisant la stéréolithographie. Dans cette technique, les particules de céramique ou de silice sont incorporées dans la résine photosensible. Après le nettoyage des parties dites vertes, le polymère est éliminé par chauffage sous atmosphère oxydante (déliantage), ce qui conduit à des pièces poreuses qui sont ensuite durcies et densifiées par frittage sous vide. Au cours de ce processus, les pièces présentent un retrait prononcé dû à la suppression du polymère. Cependant, il a été démontré que ce retrait est isotrope, ce qui permet de conserver les détails fins créés lors de l’impression. Un tel processus permettra d’améliorer nos inserts pour une compatibilité avec les températures élevées et les environnements difficiles.
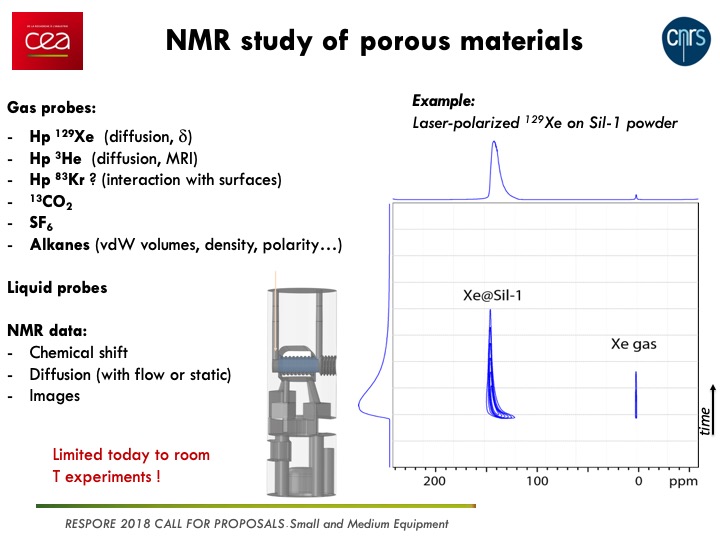
Thématiques :
Collaborations :